The Comprehensive Guide to Plastic Injection Molding for Businesses
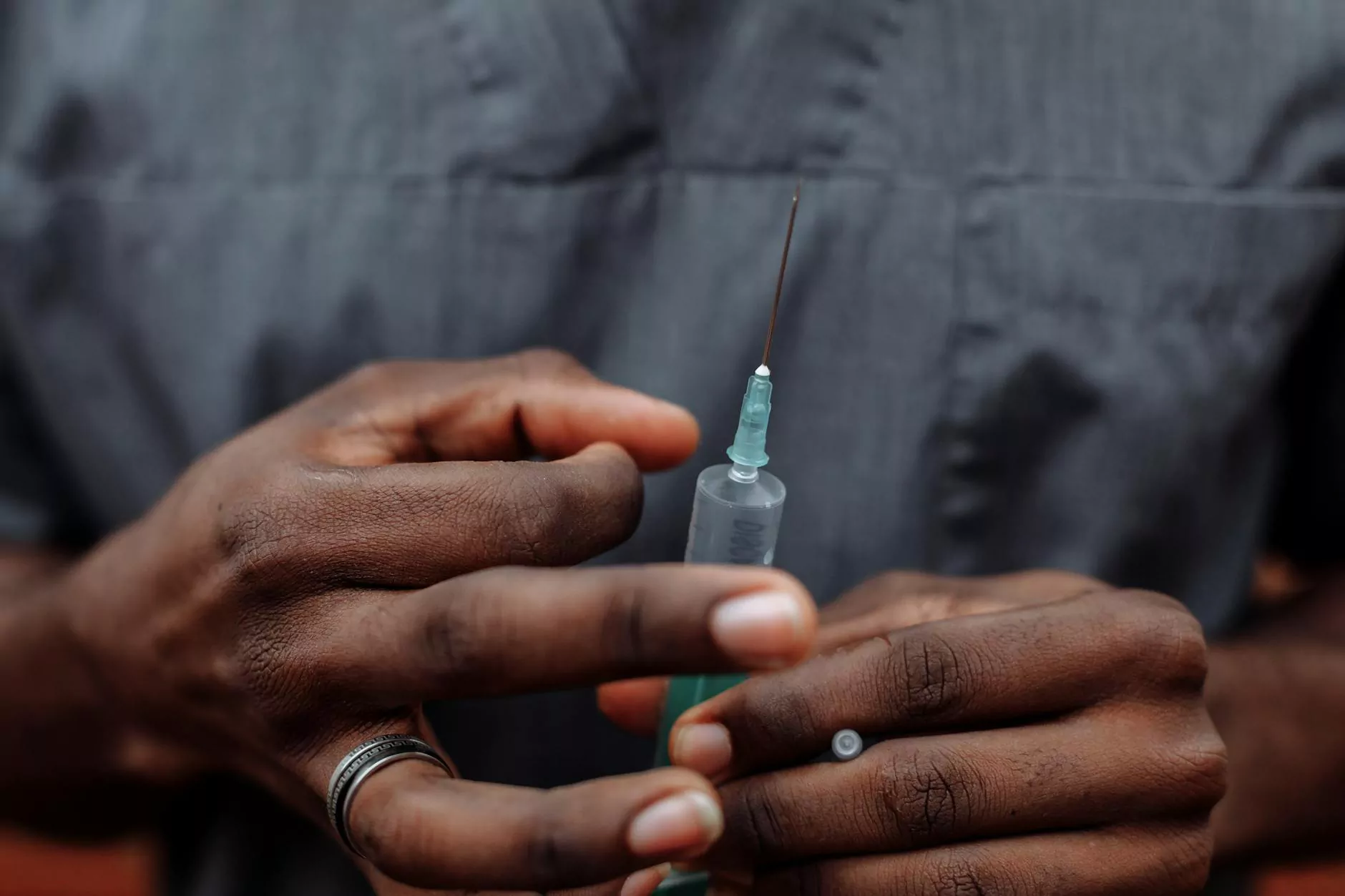
Plastic injection molding has firmly established itself as one of the most efficient and versatile manufacturing processes in the world. For businesses looking to create plastic components and products in an economical and scalable manner, understanding this technique is crucial. This article delves into the details of plastic injection molding, outlining its benefits, applications, and implications for various industries, particularly in the realm of metal fabrication and beyond.
Understanding Plastic Injection Molding
Plastic injection molding is a manufacturing process that involves injecting molten plastic into a mold to create specific shapes and designs. This technique allows for rapid production of a high volume of parts with precision and repeatability. The process typically includes the following steps:
- Material Selection: Choosing the right type of plastic is essential. Popular materials include ABS, polycarbonate, and nylon, each offering distinct properties.
- Mold Creation: Molds are custom-designed and manufactured to the specifications of the product, which can be made from steel, aluminum, or other materials.
- Injection: The selected plastic granules are heated until they melt and are then injected into the mold under high pressure.
- Cooling: The injected plastic cools and solidifies to take the shape of the mold.
- Finishing: Once cooled, the mold opens, and the finished product is ejected, often requiring additional finishing steps like trimming or coating.
The Advantages of Plastic Injection Molding
The benefits of plastic injection molding extend beyond just the simplicity of the process. Here are some of the key advantages:
- High Efficiency: Once the mold is created, producing parts is incredibly fast, leading to increased production rates.
- Cost-Effectiveness: The ability to produce large volumes while minimizing waste helps in reducing overall costs.
- Design Flexibility: Complex shapes and intricate designs can be achieved, making it possible to innovate in product development.
- Material Versatility: A wide range of plastic types can be used, which enables businesses to choose materials that best suit their product requirements.
- Minimal Waste Production: The process is designed to use materials efficiently, resulting in minimal scrap waste.
- Excellent Surface Finish: Parts produced via injection molding typically have a high-quality surface finish without the need for extensive post-processing.
Applications of Plastic Injection Molding
Various industries benefit from plastic injection molding, including:
1. Automotive Industry
The automotive sector utilizes plastic injection molding for producing a variety of components, from dashboards to intricate assemblies. The process allows for lightweight and durable parts that can withstand the rigors of daily use.
2. Consumer Electronics
Many devices, such as smartphones and laptops, feature casings and components made through plastic injection molding. The precision in design allows for high performance and aesthetic appeal.
3. Medical Devices
The medical field heavily relies on injection molded components for devices, ensuring they meet stringent safety and performance standards. Products such as syringes, housings, and intricate parts can be mass-produced with precision.
4. Household Goods
From containers to appliances, many household products owe their existence to plastic injection molding. This process enables manufacturers to produce durable and lightweight products at scale.
5. Toys
The toy industry is also a major beneficiary of injection molding. Colorful and complex designs are easily attainable while ensuring safety and compliance with regulations.
Key Considerations When Using Plastic Injection Molding
While plastic injection molding offers numerous advantages, several factors must be considered to maximize its effectiveness:
1. Initial Mold Costs
The cost of creating molds can be significant; however, this cost is offset by the savings achieved during mass production. It is crucial to plan for this upfront investment.
2. Design for Manufacturability
Effective design helps in creating molds that are not only functional but also economical to produce. Understanding design principles and inputs from manufacturing experts can streamline the process significantly.
3. Material Selection
Choosing the right material based on its properties—such as strength, flexibility, and cost—is vital in achieving the desired outcome. Collaborating with experienced suppliers can aid in selecting the best options.
Future Trends in Plastic Injection Molding
As technology advances, plastic injection molding is also evolving. Here are some trends that are likely to shape the future of this manufacturing process:
1. Sustainable Practices
With increasing awareness around sustainability, manufacturers are seeking more eco-friendly materials and processes. Biodegradable plastics and recycling initiatives are on the rise.
2. Automation and Robotics
Automation is enhancing the efficiency of injection molding processes. The integration of robotics within manufacturing lines can reduce labor costs and improve product consistency.
3. Advanced Technologies
Technologies such as 3D printing are finding their way into mold production, allowing for faster prototyping and reduced time-to-market.
4. Smart Manufacturing
The Internet of Things (IoT) is poised to revolutionize injection molding by enabling real-time monitoring and data collection, which can improve production efficiency and quality control.
How to Choose a Reliable Plastic Injection Molding Partner
Selecting the right plastic injection molding partner is crucial for ensuring quality and reliability. Consider the following factors:
- Experience and Expertise: Look for companies with a proven track record in the industry and specific experience in your product category.
- Custom Solutions: Ensure that the manufacturer is willing to provide tailored solutions that meet your specific design and functional requirements.
- Technical Capabilities: Evaluate their technological capabilities, including machinery, software, and processes used in production.
- Quality Control: A robust quality assurance program is critical to ensure the consistency and reliability of your products.
- Customer Support: Reliable customer service and support can make a significant difference in communication and problem resolution.
Conclusion
In summary, plastic injection molding stands as a pillar of modern manufacturing, providing businesses with the tools necessary to innovate and produce efficiently. By understanding its processes, benefits, and future trends, companies can leverage this technology to enhance their products and ensure sustained growth. Whether you are a startup or an established corporation, embracing plastic injection molding could very well be the key to unlocking new opportunities in your industry.
For further information on how plastic injection molding can benefit your business, visit deepmould.net.